VERWERKING VAN GRANIETAGGREGATEN
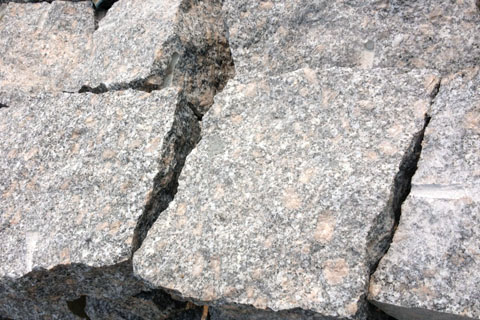
ONTWERPOUTPUT
Volgens de behoeften van de klant
MATERIAAL
Het is geschikt voor het primaire, secundaire en fijne vermalen van harde rotsmaterialen, zoals basalt, graniet, orthoklaas, gabbro, diabaas, dioriet, peridotiet, andesiet, ryoliet, enz.
SOLLICITATIE
Het is geschikt voor toepassing in waterkracht-, snelweg- en stedelijke bouw, enz.
UITRUSTING
Kaakbreker, hydraulische kegelbreker, zandmaker, triltoevoer, trilzeef, transportband.
INTRODUCTIE VAN BASALT
Graniet is uniform van structuur, stijf van structuur en mooi van kleur.Het is een soort duurzaam aggregaat van hoge kwaliteit en wordt beschouwd als de koning der stenen.In de bouwsector kan graniet overal voorkomen, van dak tot vloer.Wanneer het wordt vermalen, kan het worden gebruikt voor de productie van cement en vulmateriaal.Graniet is moeilijk te verweren en het uiterlijk en de kleur kunnen meer dan een eeuw behouden blijven.Behalve dat het wordt gebruikt als decoratief bouwmateriaal en als vloer van de hal, is het de eerste keuze voor openluchtsculpturen.Omdat graniet zeldzaam is, kan het de waarde toevoegen van gebouwen waarvan de vloeren van graniet zijn gemaakt.Bovendien kan het natuurlijke aanrechtblad hitte verdragen, waardoor dit vaak voorrang krijgt bij verschillende bouwmaterialen.
BASISPROCES VAN DE PRODUCTIE-INSTALLATIE VAN GRANIET
De productielijn voor het breken van graniet is verdeeld in drie fasen: grof breken, middelfijn breken en zeven.
De eerste fase: grof breken
De granietsteen die van de berg wordt geblazen, wordt door de trillende feeder gelijkmatig door de silo gevoerd en naar de kaakbreker getransporteerd voor grove vermaling.
De tweede fase: medium en fijn vermalen
De grof gemalen materialen worden gezeefd door een trilzeef en vervolgens via een transportband naar de kegelbreker getransporteerd voor middelmatige en fijne vermaling.
De derde fase: screening
De medium en fijn gemalen stenen worden via een transportband naar de trilzeef getransporteerd om stenen met verschillende specificaties te scheiden.De stenen die voldoen aan de eisen van de deeltjesgrootte van de klant worden via de transportband naar de stapel eindproduct getransporteerd.De impactbreker verplettert opnieuw en vormt een gesloten circuitcyclus.
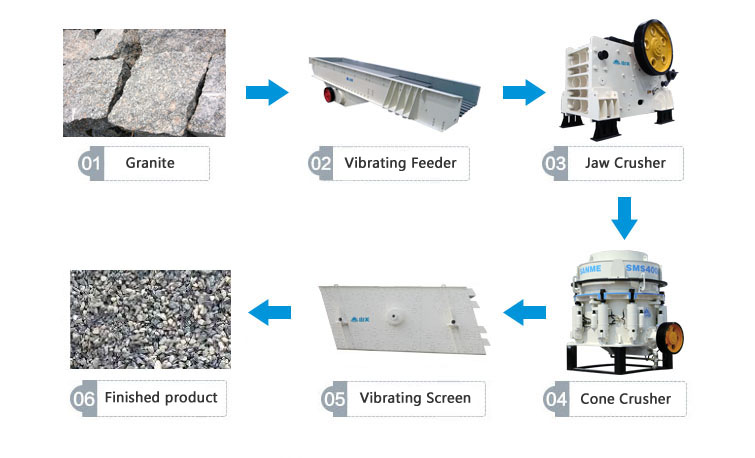
BASISPROCES VAN DE INSTALLATIE VOOR HET MAKEN VAN GRANIETZAND
Het proces voor het maken van granietzand is verdeeld in vier fasen: grof breken, middelfijn breken, zand maken en zeven.
De eerste fase: grof breken
De granietsteen die van de berg wordt geblazen, wordt door de trillende feeder gelijkmatig door de silo gevoerd en naar de kaakbreker getransporteerd voor grove vermaling.
De tweede fase: middelfijn vermalen
De grof gemalen materialen worden gezeefd door een trilzeef en vervolgens via een transportband naar de kegelbreker getransporteerd voor middelmatige vermaling.De gebroken stenen worden via een transportband naar de trilzeef getransporteerd om verschillende specificaties van stenen uit te zeven.De stenen die voldoen aan de eisen van de deeltjesgrootte van de klant worden via de transportband naar de stapel eindproduct getransporteerd.De kegelbreker vermaalt opnieuw en vormt een gesloten circuit.
De derde fase: zand maken
Het gebroken materiaal is groter dan de grootte van het tweelaagse scherm en de steen wordt via de transportband naar de zandmakermachine getransporteerd voor fijn vermalen en vormgeven.
De vierde fase: screening
De fijngemalen en opnieuw gevormde materialen worden door een trilzeef gezeefd op grof zand, middelmatig zand en fijn zand.
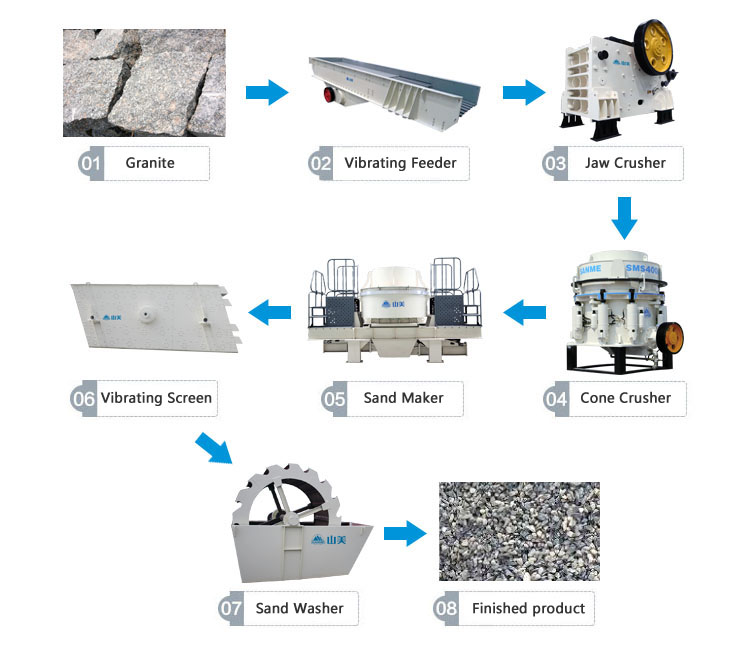
Let op: Voor het zandpoeder waaraan strenge eisen worden gesteld, kan achter het fijne zand een zandwasmachine worden geplaatst.Het afvalwater dat uit de zandwasmachine wordt geloosd, kan worden teruggewonnen door de fijnzandrecyclage-inrichting.Enerzijds kan het de milieuvervuiling verminderen, anderzijds kan het de zandproductie vergroten.
Technische beschrijving
1. Dit proces is ontworpen volgens de door de klant opgegeven parameters.Dit stroomschema is uitsluitend ter referentie.
2. De feitelijke constructie moet worden aangepast aan het terrein.
3. Het moddergehalte van het materiaal mag niet hoger zijn dan 10%, en het moddergehalte zal een belangrijke impact hebben op de output, de uitrusting en het proces.
4. SANME kan technologische procesplannen en technische ondersteuning bieden volgens de werkelijke behoeften van klanten, en kan ook niet-standaard ondersteunende componenten ontwerpen volgens de feitelijke installatieomstandigheden van klanten.