فرآوری سنگدانه های گرانیت
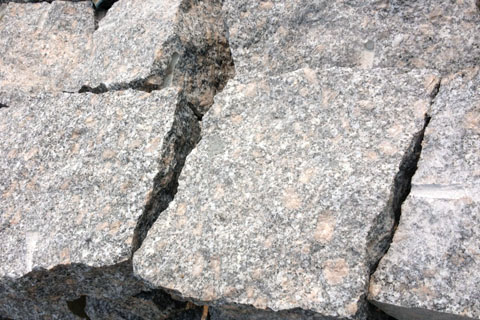
خروجی طراحی
با توجه به نیاز مشتری
مواد
برای خرد کردن اولیه، ثانویه و ریز مواد سنگ سخت مانند بازالت، گرانیت، ارتوکلاز، گابرو، دیاباز، دیوریت، پریدوتیت، آندزیت، ریولیت و غیره مناسب است.
کاربرد
برای کاربرد در نیروگاه های آبی، بزرگراه ها و ساخت و سازهای شهری و غیره مناسب است.
تجهیزات
سنگ شکن فکی، سنگ شکن مخروطی هیدرولیک، ماسه ساز، فیدر ویبره، صفحه ارتعاشی، نوار نقاله.
معرفی بازالت
گرانیت از نظر ساختار یکنواخت، از نظر بافت سفت و از نظر رنگ زیبا است.این یک نوع سنگدانه بادوام باکیفیت است و پادشاه سنگ ها محسوب می شود.در صنعت ساختمان، گرانیت می تواند در همه جا از سقف تا کف وجود داشته باشد.در حال خرد شدن، می توان از آن برای تولید سیمان و مواد پرکننده استفاده کرد.هوازدگی برای گرانیت دشوار است و ظاهر و رنگ آن می تواند بیش از یک قرن باقی بماند.علاوه بر استفاده به عنوان مصالح ساختمانی تزئینی و کف سالن، اولین انتخاب مجسمه های فضای باز است.از آنجا که گرانیت کمیاب است، می تواند ارزش ساختمان هایی را که کف آنها از گرانیت ساخته شده است، بیافزاید.علاوه بر این، کانتر طبیعی می تواند گرما را تحمل کند، بنابراین اغلب در میان مصالح ساختمانی مختلف اولویت دارد.
فرآیند پایه کارخانه تولید سنگ شکن گرانیت
خط تولید سنگ شکن گرانیت به سه مرحله خرد کردن درشت، خرد کردن متوسط ریز و غربال تقسیم می شود.
مرحله اول: خرد کردن درشت
سنگ گرانیت منفجر شده از کوه به طور یکنواخت توسط فیدر ارتعاشی از طریق سیلو تغذیه می شود و برای خرد کردن درشت به سنگ شکن فکی منتقل می شود.
مرحله دوم: خرد کردن متوسط و ریز
مواد درشت خرد شده توسط صفحه ارتعاشی غربال می شوند و سپس توسط نوار نقاله به سنگ شکن مخروطی برای خرد کردن متوسط و ریز منتقل می شوند.
مرحله سوم: غربالگری
سنگ های متوسط و ریز خرد شده از طریق نوار نقاله به صفحه ارتعاشی منتقل می شوند تا سنگ هایی با مشخصات مختلف جدا شوند.سنگ هایی که نیازهای اندازه ذرات مشتری را برآورده می کنند از طریق نوار نقاله به شمع محصول نهایی منتقل می شوند.سنگ شکن ضربه ای دوباره خرد می شود و یک چرخه مدار بسته را تشکیل می دهد.
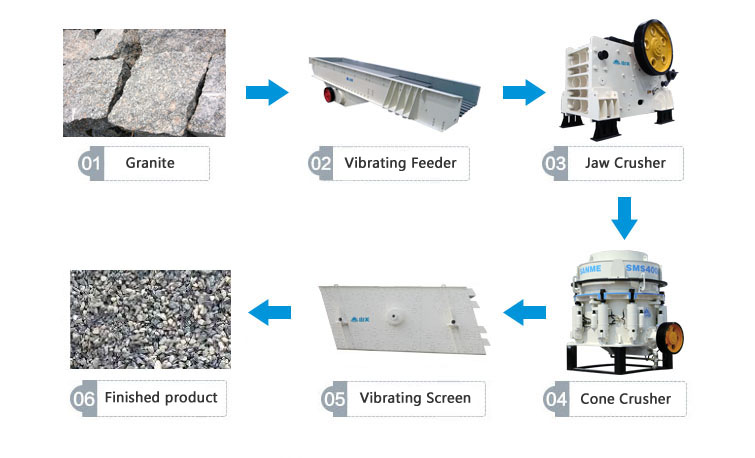
فرآیند اساسی کارخانه شن و ماسه سازی گرانیت
فرآیند ساخت ماسه گرانیت به چهار مرحله تقسیم می شود: خرد کردن درشت، خرد کردن متوسط ریز، ماسه سازی و غربالگری.
مرحله اول: خرد کردن درشت
سنگ گرانیت منفجر شده از کوه به طور یکنواخت توسط فیدر ارتعاشی از طریق سیلو تغذیه می شود و برای خرد کردن درشت به سنگ شکن فکی منتقل می شود.
مرحله دوم: خرد کردن متوسط
مواد درشت خرد شده توسط صفحه ارتعاشی غربال می شوند و سپس توسط نوار نقاله به سنگ شکن مخروطی برای خرد کردن متوسط منتقل می شوند.سنگ های خرد شده از طریق نوار نقاله به صفحه ارتعاشی منتقل می شوند تا مشخصات مختلف سنگ ها را از بین ببرند.سنگ هایی که نیازهای اندازه ذرات مشتری را برآورده می کنند از طریق نوار نقاله به شمع محصول نهایی منتقل می شوند.سنگ شکن مخروطی دوباره خرد می شود و یک چرخه مدار بسته را تشکیل می دهد.
مرحله سوم: ماسه سازی
مواد خرد شده بزرگتر از اندازه صفحه دو لایه است و سنگ از طریق نوار نقاله برای خرد کردن و شکل دادن به دستگاه شن و ماسه ساز منتقل می شود.
مرحله چهارم: غربالگری
مواد ریز خرد شده و تغییر شکل داده شده توسط صفحه ارتعاشی برای ماسه درشت، ماسه متوسط و ماسه ریز غربال می شوند.
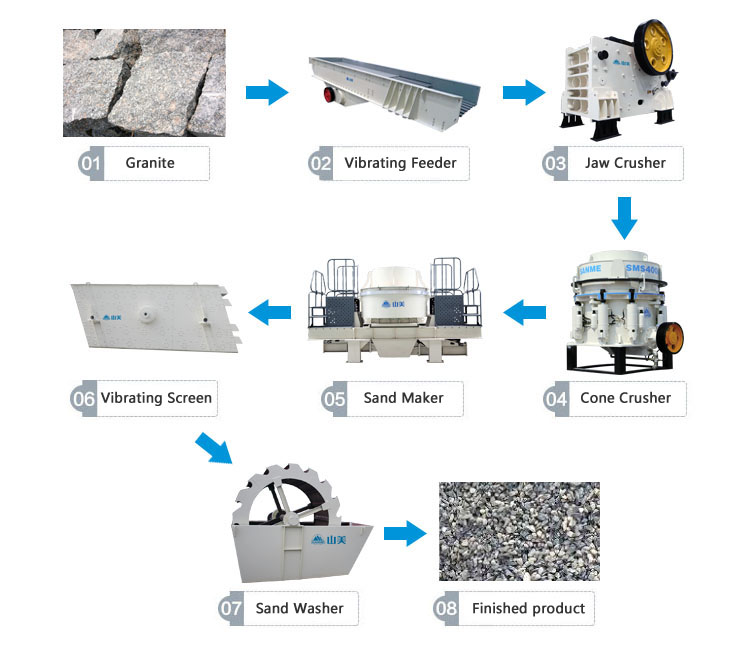
توجه: برای پودر ماسه با الزامات سخت، می توان یک ماشین لباسشویی شن و ماسه را پشت ماسه ریز اضافه کرد.فاضلاب تخلیه شده از ماشین لباسشویی شن و ماسه را می توان توسط دستگاه بازیافت شن و ماسه ریز بازیافت کرد.از یک طرف می تواند آلودگی های زیست محیطی را کاهش دهد و از طرف دیگر باعث افزایش تولید شن و ماسه می شود.
اطلاعات تکنیکی
1. این فرآیند با توجه به پارامترهای ارائه شده توسط مشتری طراحی شده است.این نمودار جریان فقط برای مرجع است.
2. ساخت و ساز واقعی باید با توجه به زمین تنظیم شود.
3. محتوای گل مواد نمی تواند از 10٪ تجاوز کند و محتوای گل تأثیر مهمی بر خروجی، تجهیزات و فرآیند خواهد داشت.
4. SANME می تواند برنامه های فرآیند فناوری و پشتیبانی فنی را با توجه به نیازهای واقعی مشتریان ارائه دهد و همچنین می تواند قطعات پشتیبانی غیر استاندارد را با توجه به شرایط نصب واقعی مشتریان طراحی کند.